MARITECHS performs hull form optimization using a parametric modeling method combined with CFD calculations. With this method, it is possible to reduce the ship’s power consumption by 3–10%, depending on the type of vessel.
To carry out the optimization calculations, the first step is to construct the ship’s hull form using parametric curves and surfaces. With this approach, the hull shape can be modified simply by changing the values of the parameters. Depending on the specific optimization problem, the parametric hull form can be developed for certain regions or for the entire vessel.
Typically, a hull form optimization will include the following steps:
- Optimized hull lines of after region, forward region and parallel body .
- Optimization of the bulbous bow shape.
For each optimizing region, we will use different objective functions. For after region we will use the objective function such as the minimum power. For tube body region and forward region, the objective function will be minimum resistance.
The optimization process will be fully automated, meaning the hull lines automatically will be generated and transferred to the CFD software for calculation. Thus, human errors will be avoided, and computation time will be greatly shortened for a very large number of cases.
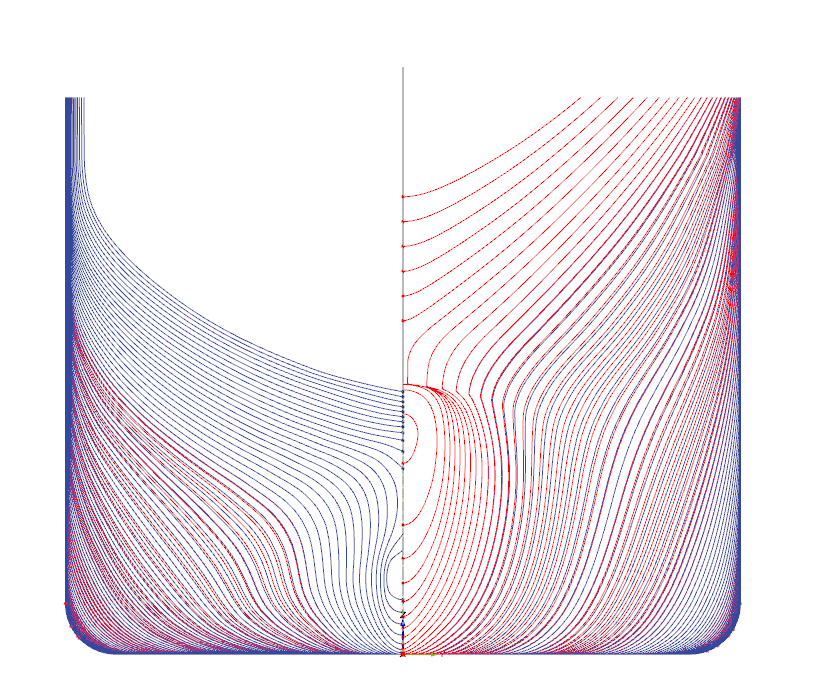
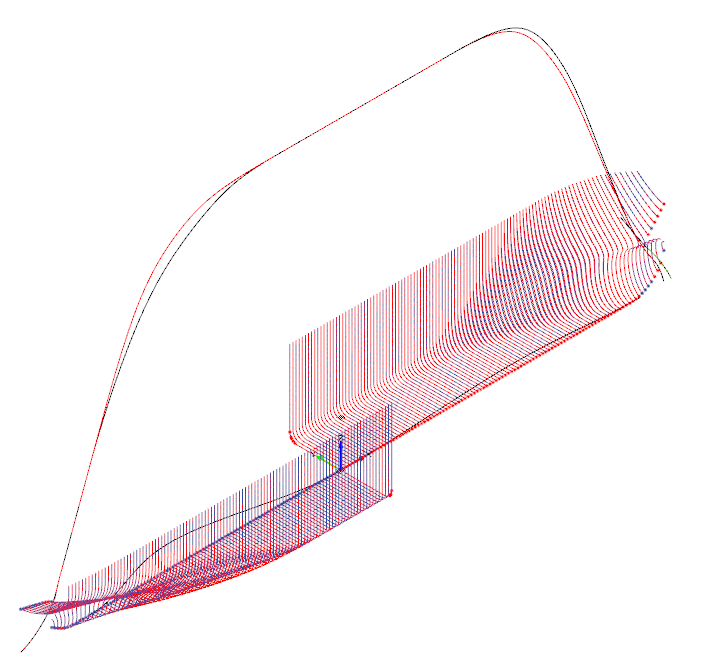
Frame section and SAC curve of original hull (red color) and modified hull (blue color)
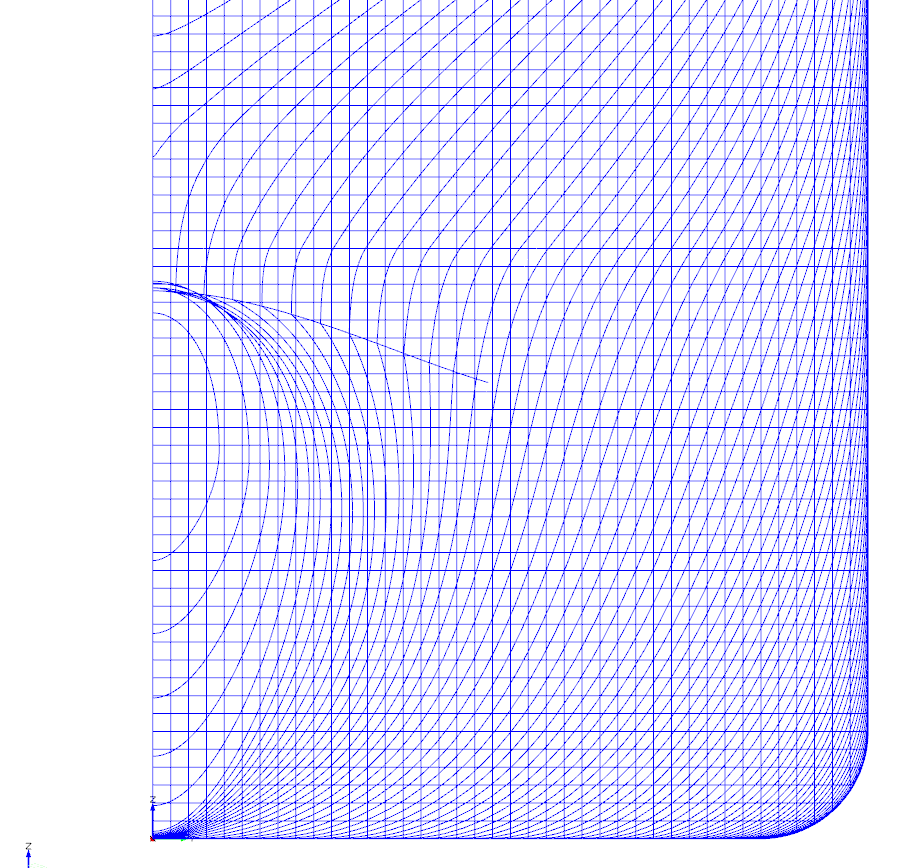
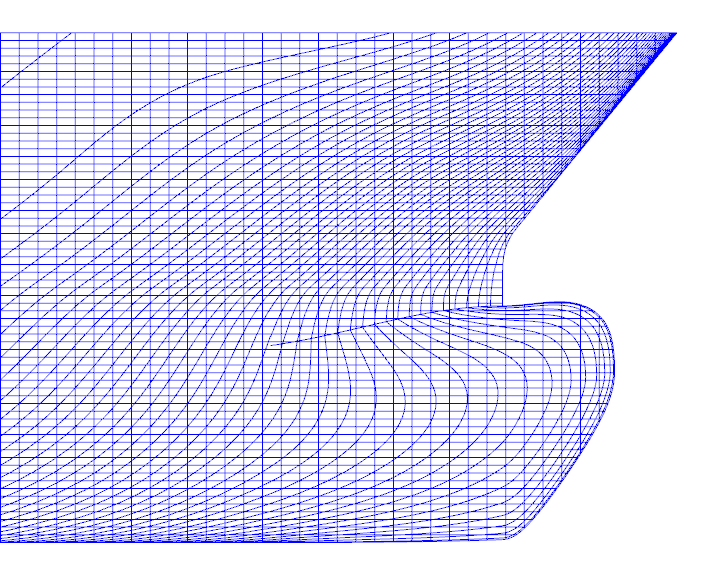
Parametric hull for bulbus bow
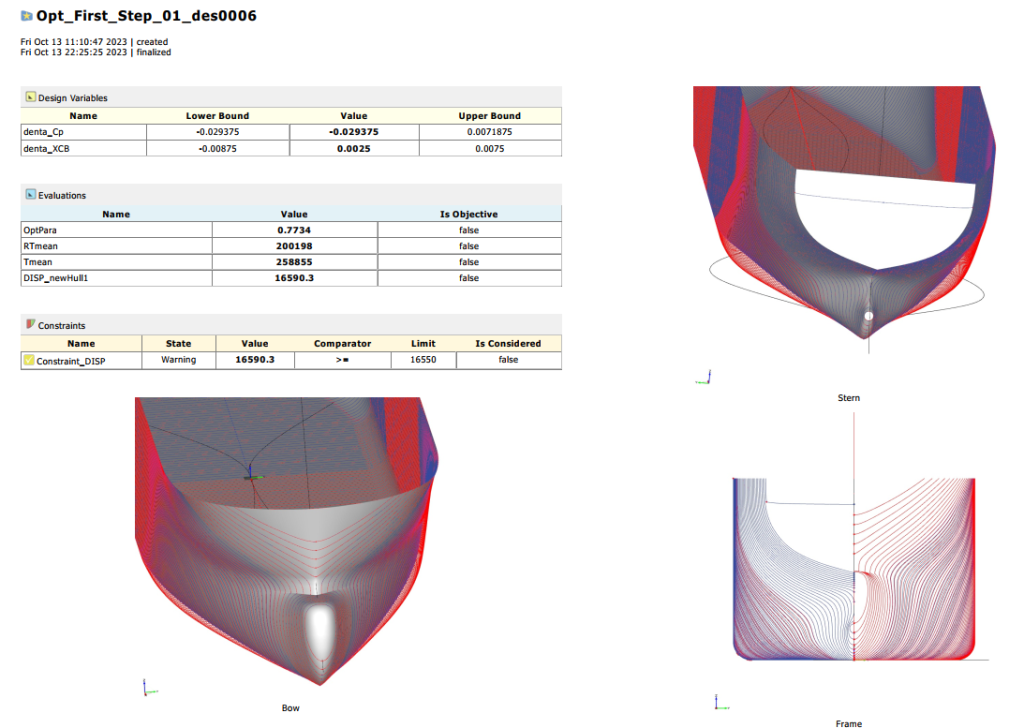
Optimizing result for parallel body, entrance region, run region

Optimizing result for bulbus bow
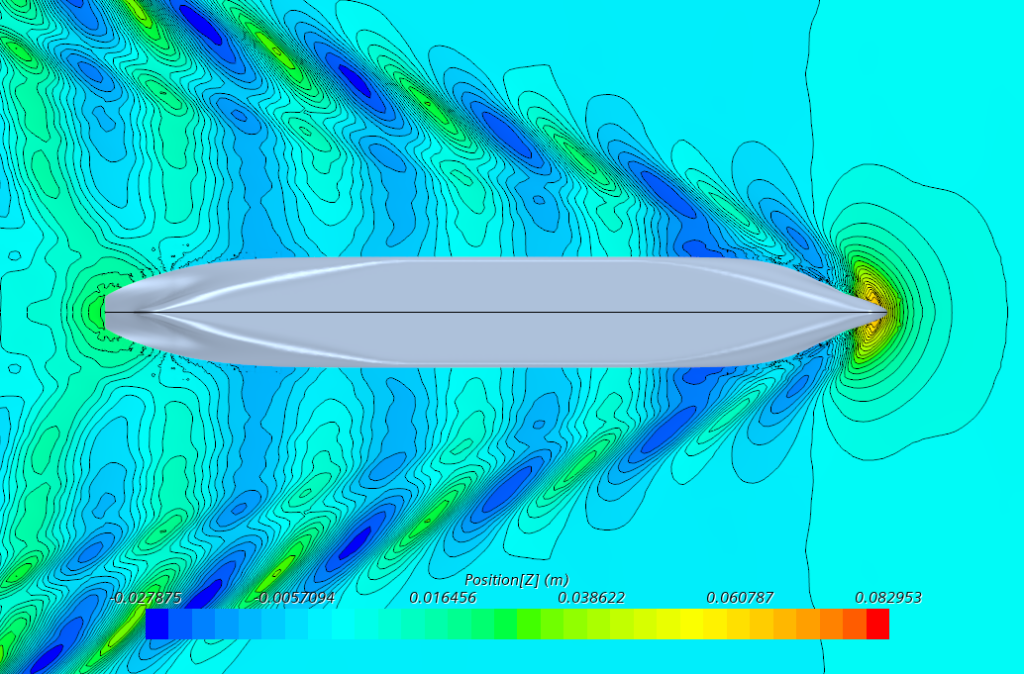
wave system for optimizing cases
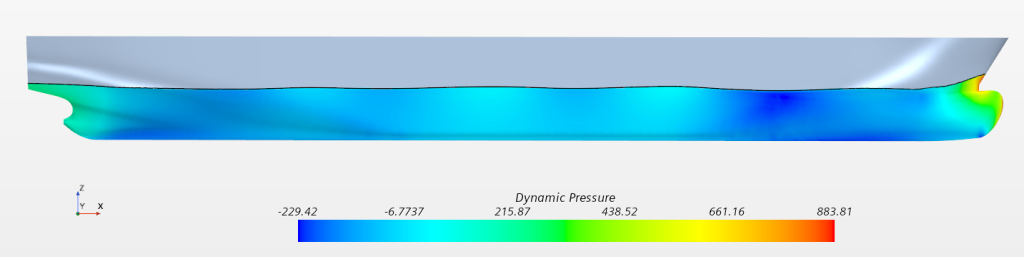
Dynamic pressure distribution for optimizing cases